A safe workplace for us all
At RECO Lift Solutions, safety and health at work means more than simply following the law or administrative obligations. As a family business though and through, we care about the safety of our employees and everyone carrying out work within and commissioned by RECO Holding. At the construction site, on the road, and in the office. A clearly formulated and well-implemented EHS Policy therefore is essential for carrying out our services. Together we make sure that parents can sit down at the table again with their family in the evenings!
The EHS Commission
Using the EHS Policy, RECO improves her company activities with regard to safety, health, and the environment, whilst enhancing the EHS awareness among employees. This is why we at RECO have set up the EHS Commission. The policy monitoring and upholding is carried out on the RECO Lift Solution premises and the project locations. Within the commission, roles within the whole organisation are represented. Management plays an exemplary role within RECO’s EHS Policy, which is why it’s also represented within the EHS Commission.
Internal communication regarding the EHS Policy
At RECO Lift Solutions, we work in an organisation structure whereby safe and healthy work conditions are key. Communication about our EHS Policy occurs in several ways. A big part of the communication is sent by the EHS Commission via email. However, in order to create EHS awareness among employees, for certain cases it’s been decided to send communication via post. This way, the home front is reached as well and accidents are brought to attention. Using this method, we at RECO Lift Solutions like to increase employees’ awareness regarding EHS. A different internal communication approach regarding EHS Policy are the toolbox meetings.
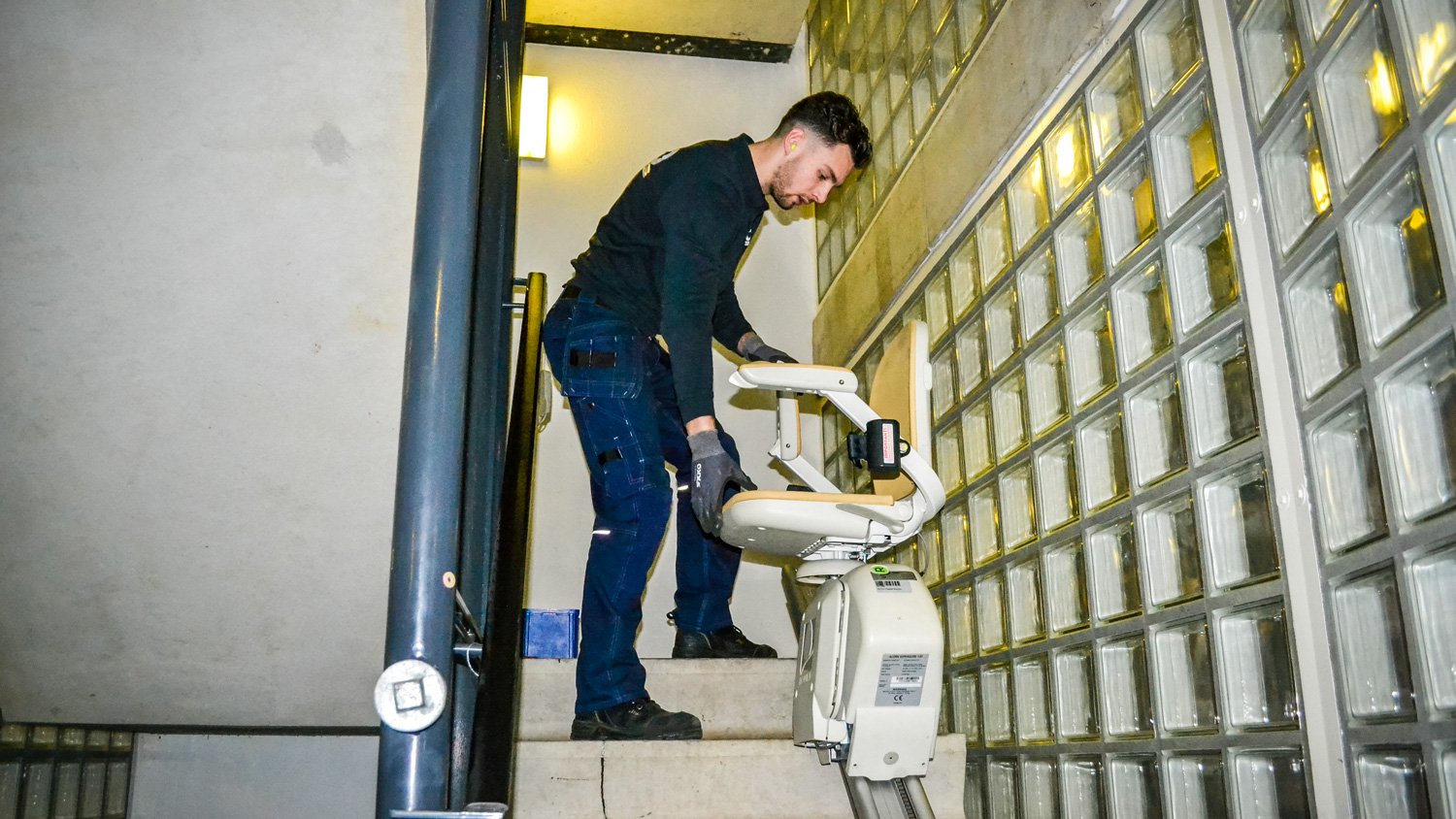
Toolbox Meetings
Every month, employees receive instructions during the compulsory toolbox meetings. Subjects discussed during these meetings include safety awareness, slippery conditions, noise, and working safely at heights. The principles are discussed and practical training is undertaken. Discipline and tidiness are also included. The toolbox meetings ensure that important subjects are discussed centrally. Another purpose of these meetings is to hear how employees are doing at work.
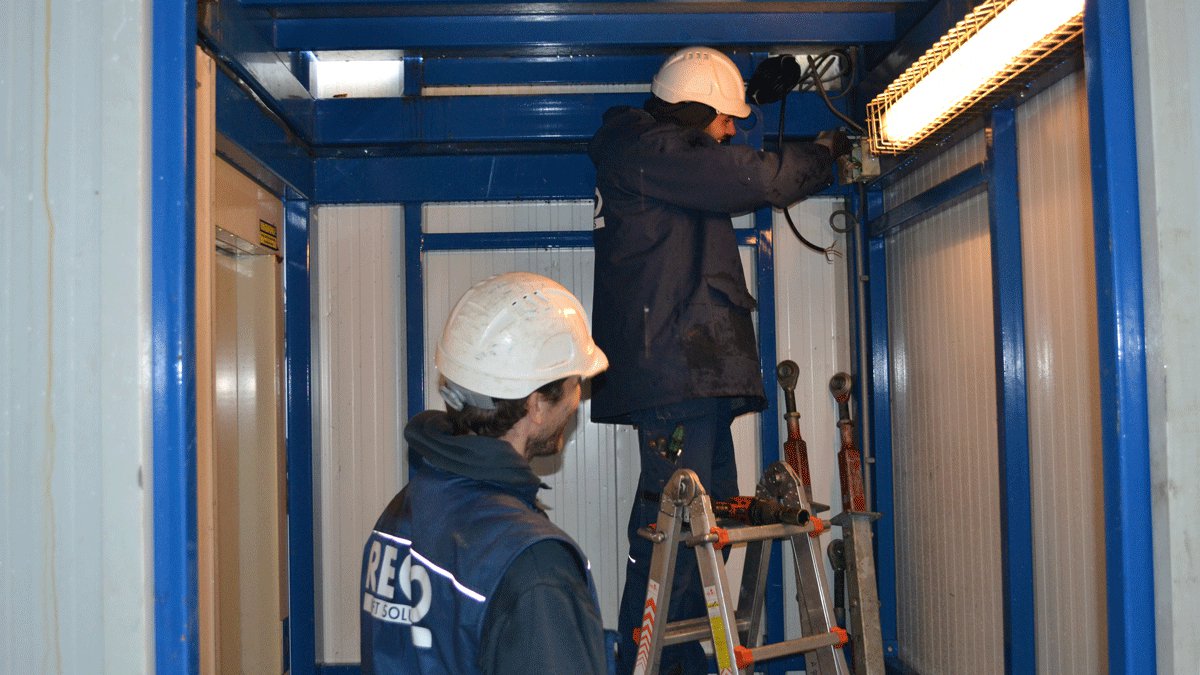
EHS incident reports, registration and investigation
Reporting a RECO Lift Solutions accident can be done via secretariaat-rls@reco.eu. Employees are regularly reminded of this via the narrowcasting screens on our locations. Reports are saved in this mailbox. In case of a serious incident, this will be discussed promptly and the resulting measures will be applied immediately. Furthermore, as a general rule a quarterly commission meeting is held to discuss all incidents. We discuss which measurements are implemented at RECO Lift Solutions to avoid recurrences. Decisions resulting from the meetings are recorded. This way, it’s guaranteed the actions will be implemented.
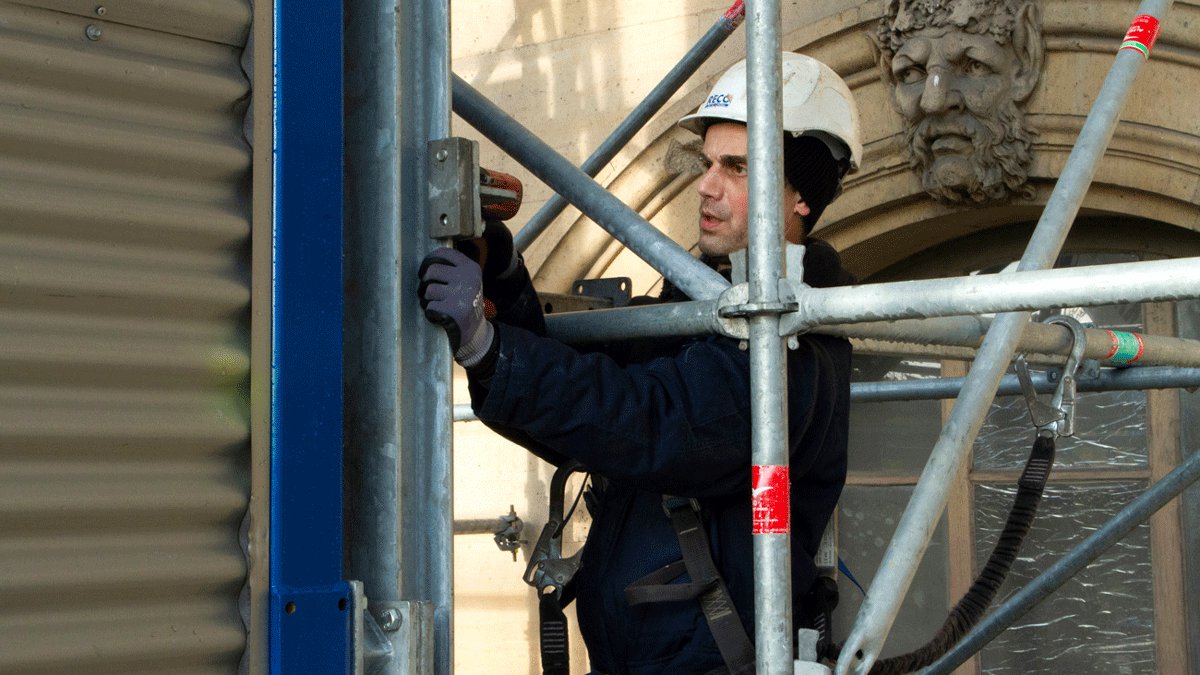
Certification of organisation and staff
RECO Lift Solutions boasts a VCA* company certification. Moreover, every engineer and driver within RECO Holding has a VCA Basic Certificate at the least. All technical and operational employees with a supervisory role have the VCA Complete Certificate.
Education, training, and instruction
At RECO Lift Solutions we think it’s important all engineers and drivers have completed the necessary courses. RECO offers these courses in house and via third parties. All lift engineers also receive the relevant education and instructions. Lift engineers are trained completely in house. Not only with regards to safety, but also in knowledge and skills concerning the materials. Every year ERO and first aid courses are organised. Moreover, we always stay on top of continually developing technologies and regulations by providing our employees with the proper training every year.
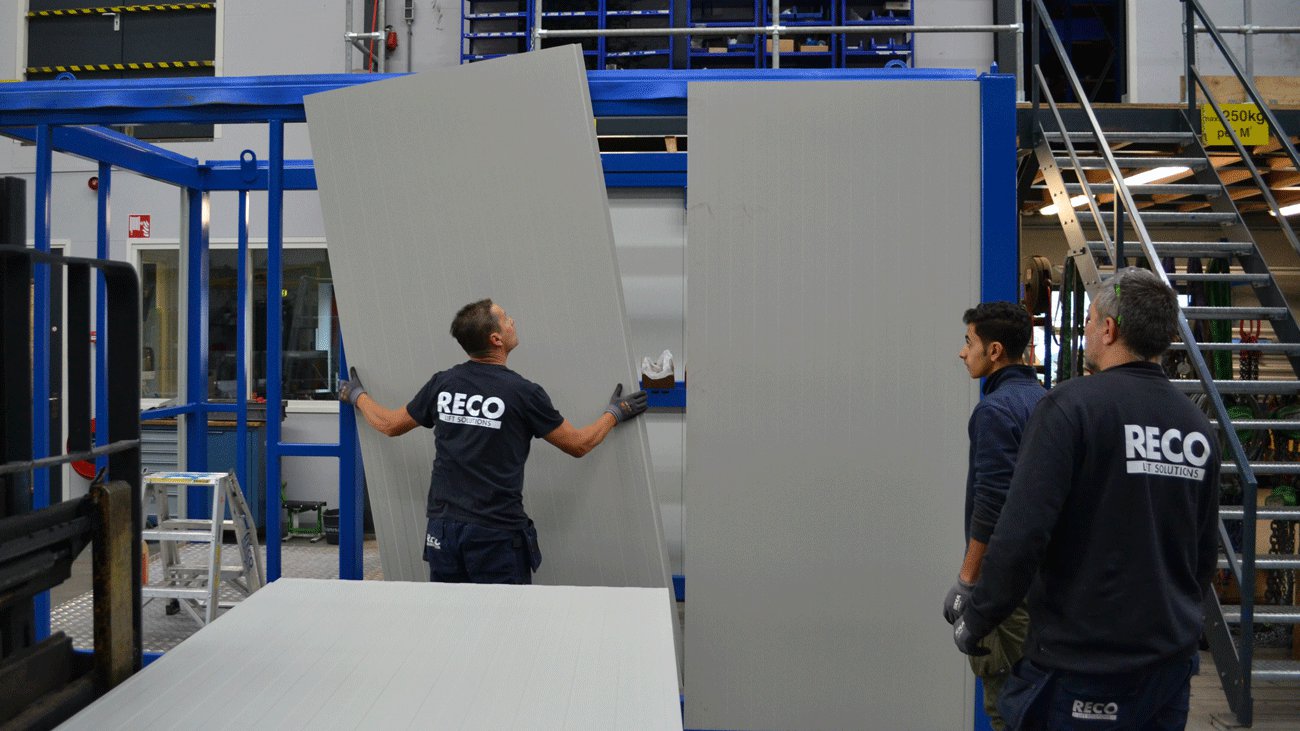
Working with inspected equipment
Our temporary passenger lifts are assessed by the Lift Institute and are assessed on site again using an installation test. Only after approval will the lift be commissioned. This also applies to all our other equipment. Only after approval will the equipment be used. This is how we ensure the safety of passenger lifts.
Our temporary passenger lifts are approved according to Machine Guideline 2006/42/EG. The certification is based on the Standards EN81-1:1998+A3 and EN81-21:2009. Our stair lifts are certified according to the International Standard for Stair Lifts BS EN81-40:2008. Furthermore, the organisations below recognise our quality and safety standards.
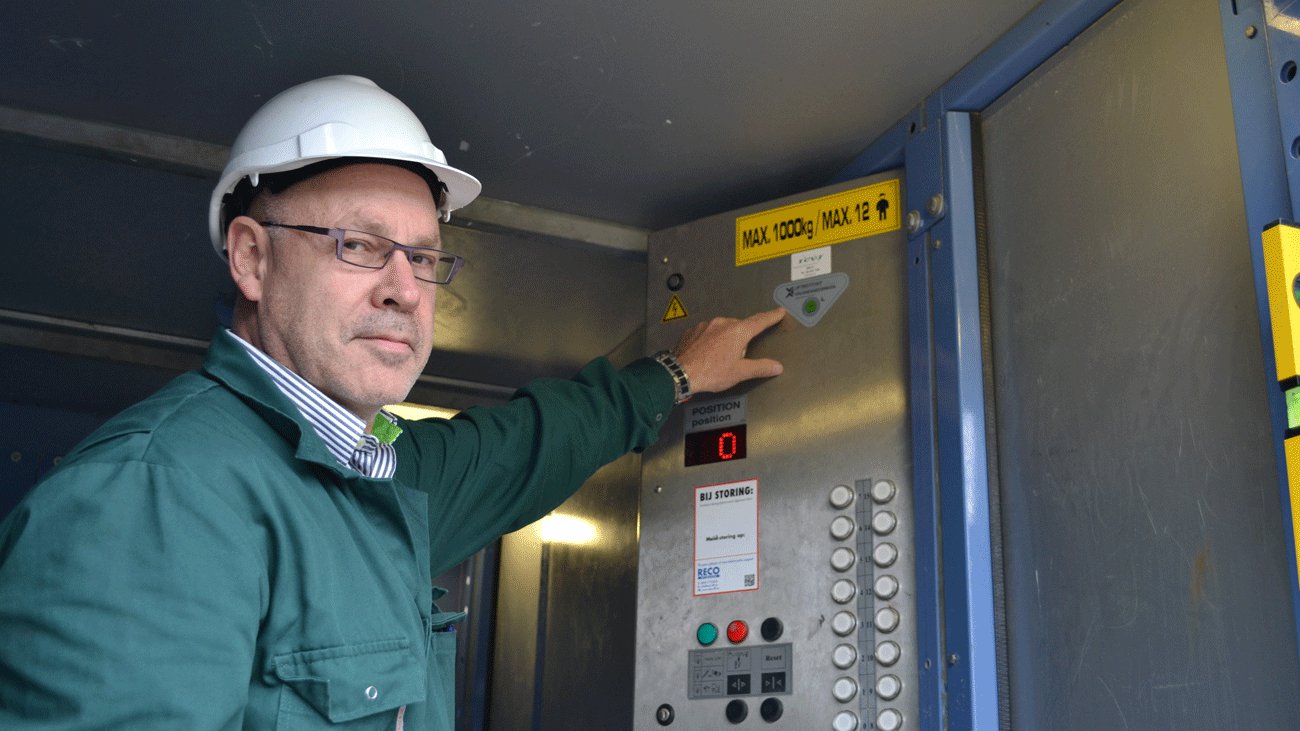
EHS Project Plan and Task Risk Analysis
Because we work in hazardous environments with third parties, we set up a EHS Project Plan for every individual project that involves manual work. This document describes which risks are involved and which control measures we take in order to guarantee the safety and health of the workers. Furthermore, at RECO we carry out a Task Risk Analysis (TRA) for high-risk projects. This analysis ensures we can carry out work more efficiently and prevents incidents from happening. Using the TRA, a work instruction is created. Within TRA, we firstly consider standard work. We also include special work activities in the analysis, such as during clearings of malfunctions, maintenance and installation.
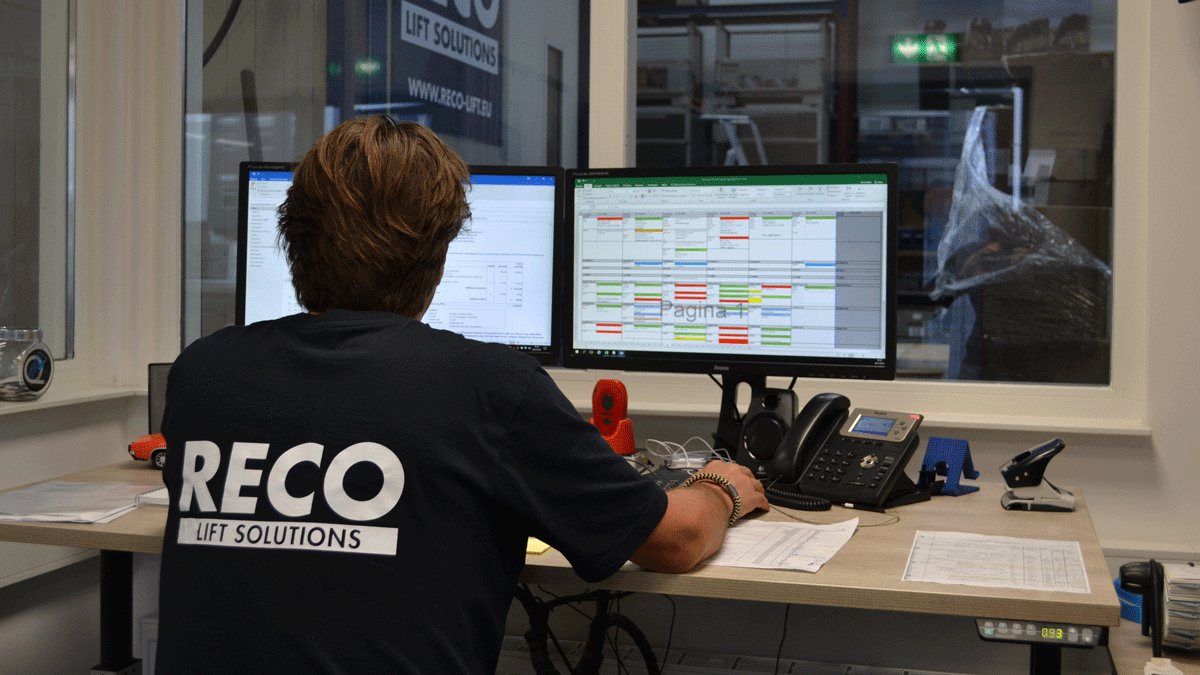
Personal protective equipment
Within RECO, every role comes with its own set of personal protective equipment (PPE). It’s used to protect employees working in hazardous environments. PPE is not allowed to hinder work and must be made to fit so it can be worn comfortably. At RECO Lift Solutions, new employees receive a complete clothing set that’s tailored to their work.
Operational employees in workplaces
- Safety shoes (during all work)
- Safety helmet (during all assembly and disassembly work)
- Hearing protection (for volumes of 80 dB and louder)
- Safety goggles (for welding and machine work)
- Full face shield (for high-pressure sprays and grinding)
- Operational employees on site
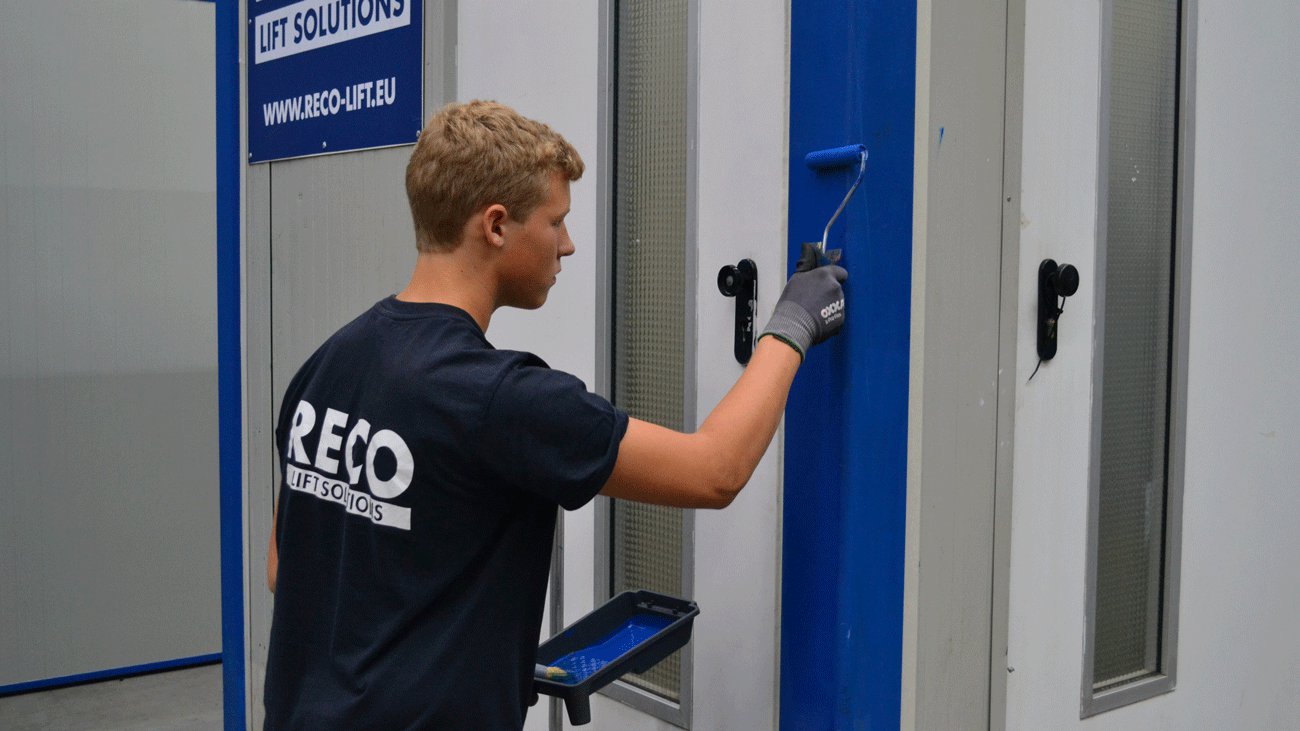
Operational employees on site
- Safety shoes (during all work)
- Safety boots (during winter)
- Safety helmet (during all assembly and disassembly work)
- Hearing protection (for volumes of 80 dB and louder)
- Safety goggles (for welding and machine work)
- Full face shield (for high-pressure sprays and grinding)
- Safety belt (for work including fall hazard without safety guards)
Operational employees logistics
- Safety shoes (during all work)
- Safety helmet (during loading and unloading)
- Hearing protection (for volumes of 80 dB and louder)
- Winter package
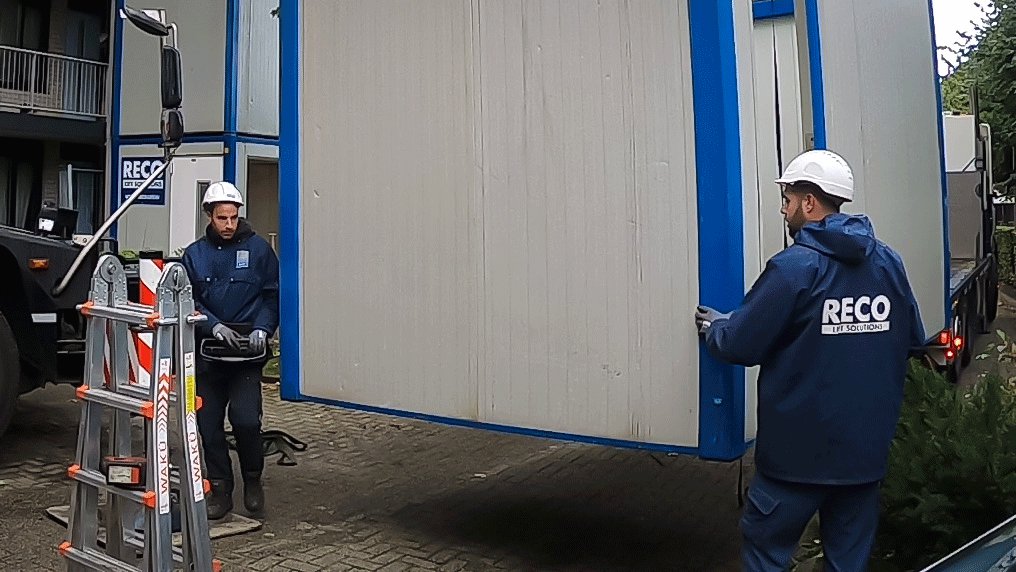
Office Staff
Safety is also a topic in the office. For instance, we ensure a safe escape route from the workplace for our office staff. Precautions for any emergency situations are also taken. New employees are informed by EROs about the appointed escape routes and locations for emergency supplies such as fire extinguishing equipment, first-aid supplies and AEDs.
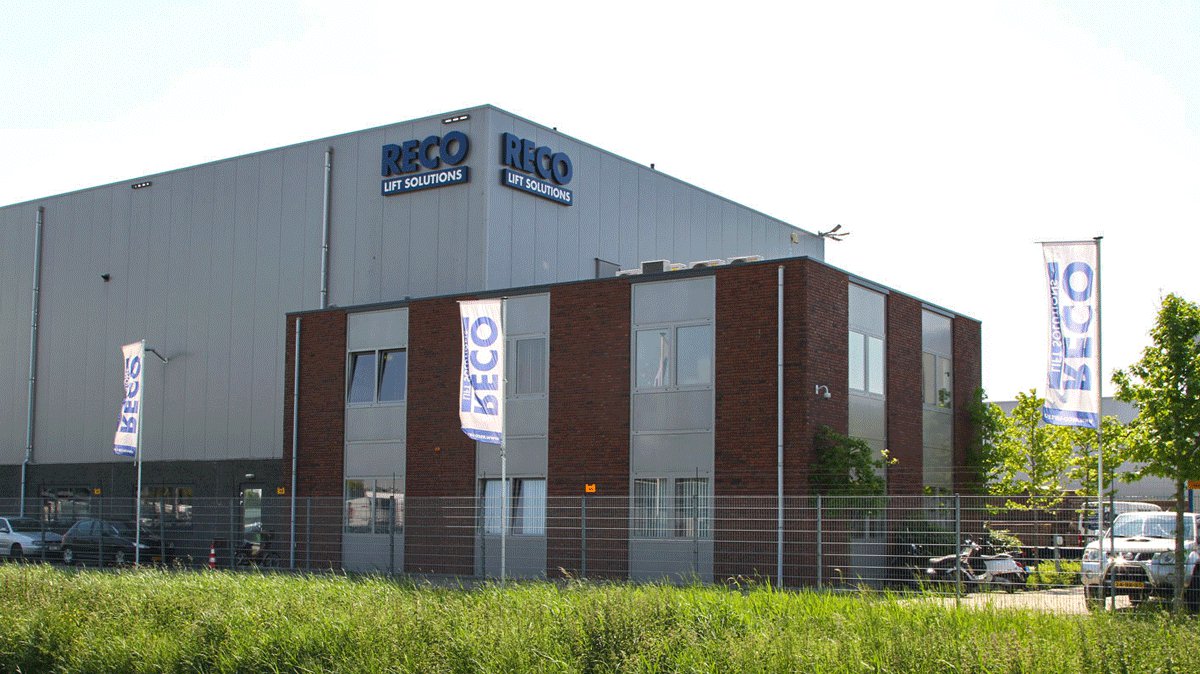
Environmental care in the workplace
The purpose of environmental care within the EHS Policy, is the prevention of environmental contamination. This means that we carefully deal with the disposal of waste materials and chemicals. Waste oil and filters are always returned and disposed of responsibly at the RECO site. The waste materials are separated by means of waste flows and submitted to a specialist for processing. Paper, cardboard, aluminium, steel, wood A, wood B, and residual waste are processed individually. Wood A is unprocessed and will be recycled into new products. Furthermore, we placed solar panels on the roofs of the workplaces and the office to supply our own power. We also offer our customers the option to make the use of diesel engine machines greener by using Blue Diesel 50. This is how we at RECO deal with our environment responsibly.
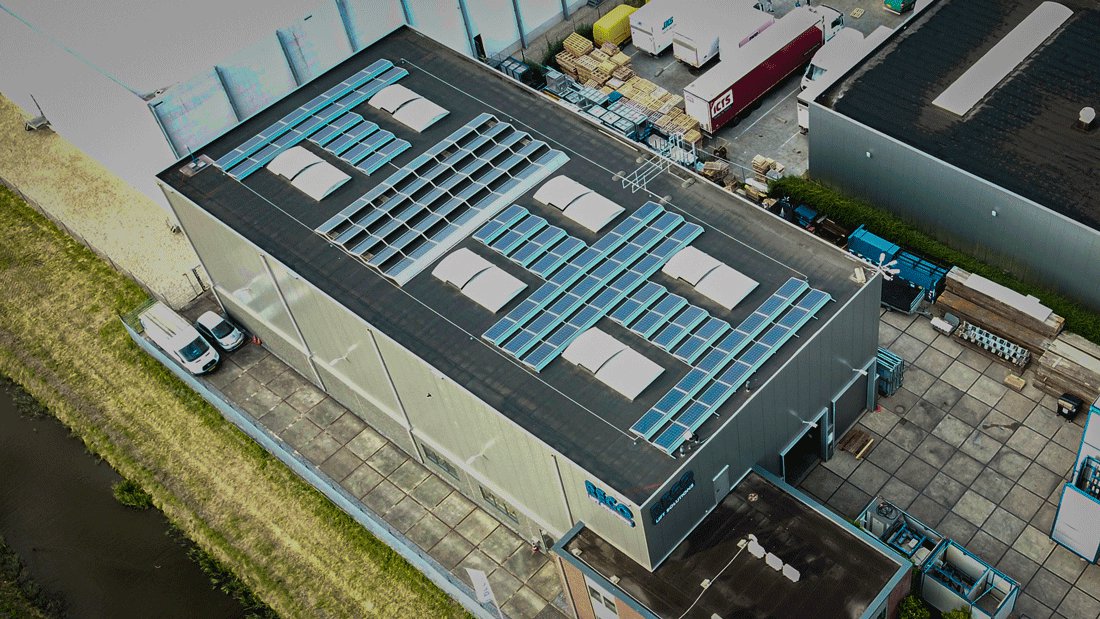
At RECO Lift Solutions, we take safety extremely serious.
We work safely or not at all!
For questions about the RECO Lift Solutions EHS Policy, please send an email to: secretariaat-rls@reco.eu.